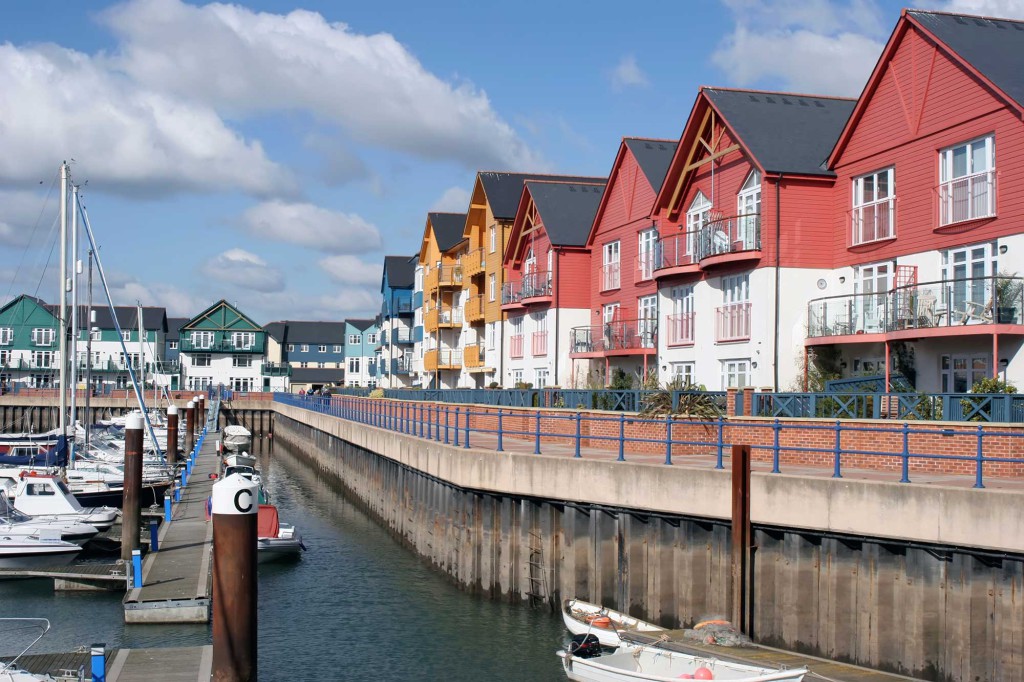
Employers will be aware that they can be held to be liable for damage or injury arising from an employee’s carelessness or recklessness. However, what happens when an employee does something so daft that it was simply not contemplated as a risk? Should the employer have foreseen that employees may do something mind-blowingly stupid and therefore guard against the risk?
In the recent Court of Appeal case of Polyflor Ltd v Health and Safety Executive, The court found that even in circumstances where one would not normally consider that an employee will do something extremely dangerous where the danger is obvious, it must nevertheless assess and control the risks to safety of a potentially careless or even a grossly careless employee.
Facts
In this case, the inured party fractured his arm whilst clearing a blockage on a roller of a granulator in-feed conveyor used to assist with recycling vinyl material. In order to check whether the adjustments made were correct, it was considered necessary to remove the guards covering the rollers. However, to allow the tracking to be checked, the machine had to be running. The injured employee obtained the necessary permission to run the machine without its guards in place. The permission was granted with no additional safety advice or review of precautions. Noticing that the running was not smooth, the employee attempted to push the conveyor belt with a spanner, which was trapped and it along with his arm were drawn into the machine.
Basis of Appeal
The Employee admitted he was foolish and that there was no need to have made contact with the belt whilst it was moving.
Polyflor appealed against its conviction for breaching Health and safety rules stating that if someone is going to do something stupid, you cannot necessarily foresee this nor stop them. They argued that because an employee could do something stupid or reckless this does not render a system of work unsafe and that there was no material risk to safety, unless an employee did something very foolish. They sought a ruling that there was no material risk and therefore there was no case to answer.
Decision
The Court however ruled that if there was some evidence of exposure to risk, it was the employer’s responsibility to show that it did all it could reasonably do to ensure that its employees were not exposed to such risk. The prosecution does not have to prove that a particular accident is foreseeable, merely that a danger has been created and that amounts to a material risk. In this case the carelessness of the employee was a material risk and the employer was liable.
Conclusions
An unguarded machine with moving parts is a clear and obvious risk. Guards are placed on machines to protect employees and others from carelessly becoming trapped or otherwise injured by them. The outcome of the case might have been different had the employer been able to offer evidence that they did all that was reasonable to avoid the risk, but they did not do so..
In determining material risk and what was foreseeable, each individual case will be different and dependent on the particular facts. However, from this case, we learn that employers should consider what measures they have in place to protect employees and others from human error, even if this is a grossly careless error, rather than discount such errors as risks because they are so unlikely to happen that they are not material or foreseeable.
This does not mean employers have to protect against every act of stupidity, but rather to look critically at its procedures and consider whether and to what degree such human error scenarios are possible and therefore need to be controlled. This case has raised the bar for employers to satisfy a court that they have taken all reasonably practicable steps and so discharged their safety obligations.